Oct. 10, 2002.
Finally after 10 straight days of rain, we are able to get started on the framing.
First wall panel UP!!!!!!!!!!!!!!!!!!!!!!!!!!!!!
You can't help but feel good when you raise the first panel on any house. Ours was no exception. I have to give special thanks to my late brother Donald, for helping so much in the construction, both physically and mentally. Don is the man in the suspenders, I'm wearing the white hat. Thanks for all your help, may you rest in peace.
Our system of SIPs are glued and nailed to the sill plate, then splined together with glue and nails. Where there is a corner, 2x6's are used to seal the end of each panel and then long screws are used to join one panel to the 2x6 of the other panel. EXTREMELY strong.
The rep from the panel manufacturer did not show up for our initial panel raising. They normally send a rep down for a day for an initial consulting. I found out later that the rep who was suppose to come down, had some medical issues and ended up in a hospital.
So our first few panels were definitely slow in rising. After that things begin to pick up steam.
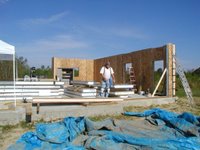
North wall up! That is one stout wall. Between the 2x6 sill plate and the 2x6's in the corners, there is no give in that wall. A football player trying to tackle it would bounce off like a rubber ball.
The headers over the doors and windows are a minor problem.
They uses what they called Versa-lam. It is a sandwich of a laminated board and Styrofoam. The laminated board part is about 1 1/2" thick. The problem is the board is high on one side of the Styrofoam and low on the other side. Finally, we realized the solution was to take the Oreo cookie apart with a Sawzall, trim the Styrofoam if necessary, and them simply re glue the Versa-lam back together. Not sure if the Versa-lam was sent from the factory in this condition or if Hurricane Lily and all of the subsequent rain caused it to warp.